Highest Quality Plastic: What Sets Premium Polymers Apart in Manufacturing
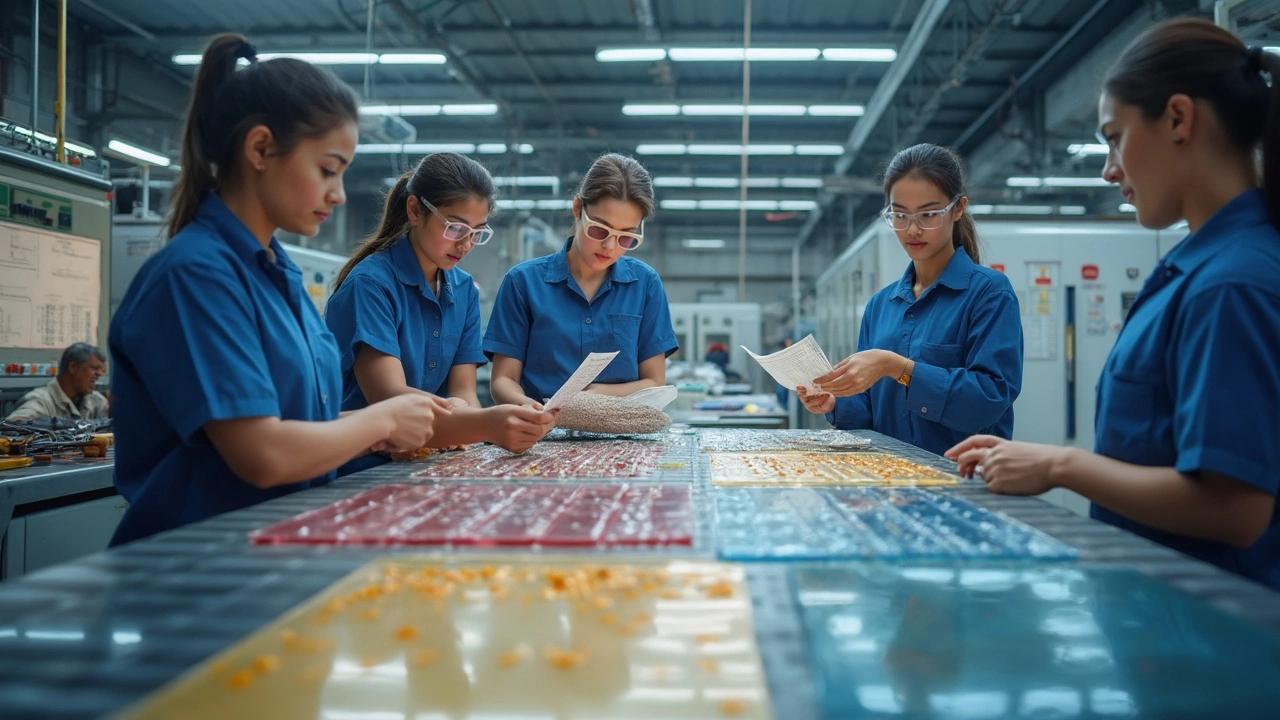
Think all plastics are the same? They’re not even close. Walk through any plastic manufacturing shop and you’ll hear opinions flying about which polymer deserves the crown. But here’s the everyday reality: the highest quality plastic isn't about having some fancy name — it's about having the right combo of durability, toughness, purity, and performance for the job at hand.
One plastic might laugh off extreme heat, while another shrugs off thousands of hits without cracking. It's like picking sports gear: what you need for cycling is totally different than for mountain climbing. That’s why the ‘best’ plastic always depends on the task.
Got a project in mind? Whether you’re building car parts, medical gear, or something that needs to hold up to intense stress, knowing how to spot truly high-quality plastic can save time, money, and a whole lot of headaches down the line. Let’s break down what quality actually means in plastic—and which ones actually earn those bragging rights.
- Defining High-Quality Plastic: More Than Just Strength
- Top Contenders: Which Plastics Reign Supreme?
- Key Properties That Separate the Best from the Rest
- Real-World Examples: Where Premium Plastics Are Used
- Choosing the Right Plastic for Your Needs
- Expert Tips for Sourcing Reliable High-Quality Plastics
Defining High-Quality Plastic: More Than Just Strength
When folks talk about the highest quality plastic, most people picture something super tough. But honestly, that's only part of the story. The real secret sauce is how a plastic keeps its good qualities in the long run, under different stress, heat, or chemicals. It's not a one-size-fits-all situation.
Manufacturers care about several other factors, not just brute strength. Here’s what typically matters when deciding if a plastic makes the cut for premium status:
- Purity: The fewer the impurities, the more predictable and strong your end product will be. Big manufacturers invest in pure resins for this very reason.
- Consistency: Good plastic acts the same way every time it's processed. Nobody wants surprises on the production line.
- Chemical resistance: Some plastics just don't crack, warp, or fade—even when they’re in tough environments packed with oils, cleaners, or water.
- Heat resistance: A high-quality plastic won’t warp or melt when things heat up, whether that's inside a kitchen appliance or a car engine.
- Impact resistance: If it takes a hit and doesn’t shatter or deform, that's premium stuff—especially in things like helmets or safety equipment.
- Appearance: Clarity, gloss, and color consistency also matter, especially for products people see or handle daily, like phone cases or car interiors.
Choosing premium polymers often comes down to which mix of these traits fits your needs best. For example, polycarbonate shines when you want real toughness and transparency—think of clear airplane windows or police riot shields. Polytetrafluoroethylene (PTFE), on the other hand, is unbeatable for chemical and heat resistance, so it's everywhere from lab equipment to frying pans.
Property | Why It Matters |
---|---|
Purity | Affects strength and safety |
Consistency | Reduces rejects and waste in manufacturing |
Chemical Resistance | Key in harsh working spaces |
Heat Resistance | Makes plastics last longer in hot spots |
Impact Resistance | Protects products and people |
The main thing to remember: the best plastic is the one that ticks off the right boxes for your application. There's no single "king of plastics"—it's about matching needs to the right material, not just chasing the toughest stuff out there.
Top Contenders: Which Plastics Reign Supreme?
When you talk about highest quality plastic, a few names always pop up in the industry. If you ask around in any plastic manufacturing plant, engineers will quickly point to the 'big hitters'—these are the materials most trusted for strength, stability, and reliability.
Polyetheretherketone (PEEK) is basically the superstar. PEEK is crazy tough, stays solid at high temperatures (up to 260°C), handles harsh chemicals like a champ, and doesn’t wear out easily. You’ll see it in gears, medical implants, and even aerospace parts. I asked a materials engineer at a medical company what they see most for demanding jobs, and he told me:
“For critical components, there’s no better option than PEEK. The consistency and safety margin are unmatched.”
Another monster on the list: Polytetrafluoroethylene (PTFE). You probably know it as Teflon. This stuff repels almost everything—acids, bases, even sticky food in frying pans. It’s the go-to for harsh chemical processing and sliding machine parts because nothing wants to stick to it.
Polycarbonate (PC) is all about strength and clarity. It’s what they use in bulletproof glass, durable eyewear, and high-end electronics. It takes a beating and stays clear, which is really rare. Fun fact: some safety goggles and riot shields are made from sheets of polycarbonate up to half an inch thick.
If you're after a material that shrugs off nearly anything you throw at it, check out Ultra-High Molecular Weight Polyethylene (UHMWPE). It’s dense, slippery, super hard to cut, and really lightweight for its toughness. You’ll find it in body armor, industrial conveyor belts, and hip replacements.
- PEEK: Top choice for medical and aerospace. Handles high temp and huge stress.
- PTFE: Non-stick king. Great for pans, valves, pipes, and bearings.
- Polycarbonate (PC): See-through and strong. Used where both properties matter.
- UHMWPE: Wears forever, barely scratches. Used in demanding environments.
Plastic Type | Max Temperature (°C) | Key Strength |
---|---|---|
PEEK | 260 | High wear and chemical resistance |
PTFE | 260 | Extreme non-stick, chemical stability |
Polycarbonate | 135 | Impact resistance, transparency |
UHMWPE | 80 | Wear resistance, low friction |
Now, if you’re eyeing the most premium polymers, these are the ones setting the standard in plastic manufacturing. Pick the right one, and you’ll save yourself years of hassle.
Key Properties That Separate the Best from the Rest
When you’re comparing highest quality plastic for manufacturing, it’s not just about picking the strongest stuff on the shelf. There are clear, measurable properties that make one polymer better than another in real-world use. You want to look at plastic like an expert, not like you’re guessing at the hardware store.
Here’s what really matters when it comes to identifying high-grade plastic for tough jobs:
- Strength and Durability: Not all plastics handle force the same way. For example, polycarbonate can take a beating—it’s what they use in bullet-resistant glass. ABS is famous for taking knocks without failing, which is why it’s in LEGO bricks and power tool housings.
- Heat Resistance: Some projects run hot. If you need high temperatures, plastics like PEEK and PTFE can handle crazy heat without warping or breaking down. Nylon melts way before these heavy-hitters even flinch.
- Chemical Resistance: If your part is exposed to oils, acids, or industrial cleaners, basic plastics just don’t cut it. Look for fluoropolymers like PTFE (aka Teflon) or Polypropylene, which are tough against most chemicals.
- Purity and Food Safety: Medical and food-grade applications demand plastics with barely any additives or random fillers. Medical-grade polycarbonate or special PE grades are tested for leaching and contamination risks.
- Clarity and Appearance: Sometimes you need see-through plastic. Acrylic and polycarbonate stand out for their glass-like clarity, while other high performers like PEEK are usually more about strength than looks.
- Consistency: Top manufacturers test every batch, making sure the melt flow and density match up. No weird surprises mid-production.
Want a quick look at how some of the best plastics stack up for high-stress manufacturing? Check this out:
Plastic | Strength | Max Service Temp (°C) | Chemical Resistance |
---|---|---|---|
Polycarbonate (PC) | High | 120 | Moderate |
PEEK | Very High | 250 | Excellent |
PTFE | Moderate | 260 | Outstanding |
ABS | Medium | 80 | Poor |
The bottom line: You need to match the plastic’s properties to what your part is going to face. If you take the time to ask for test certifications (ISO or ASTM), you’ll know you’re getting highest quality plastic—not just somebody’s sales pitch. No manufacturer cuts corners on quality and gets away with it long-term.
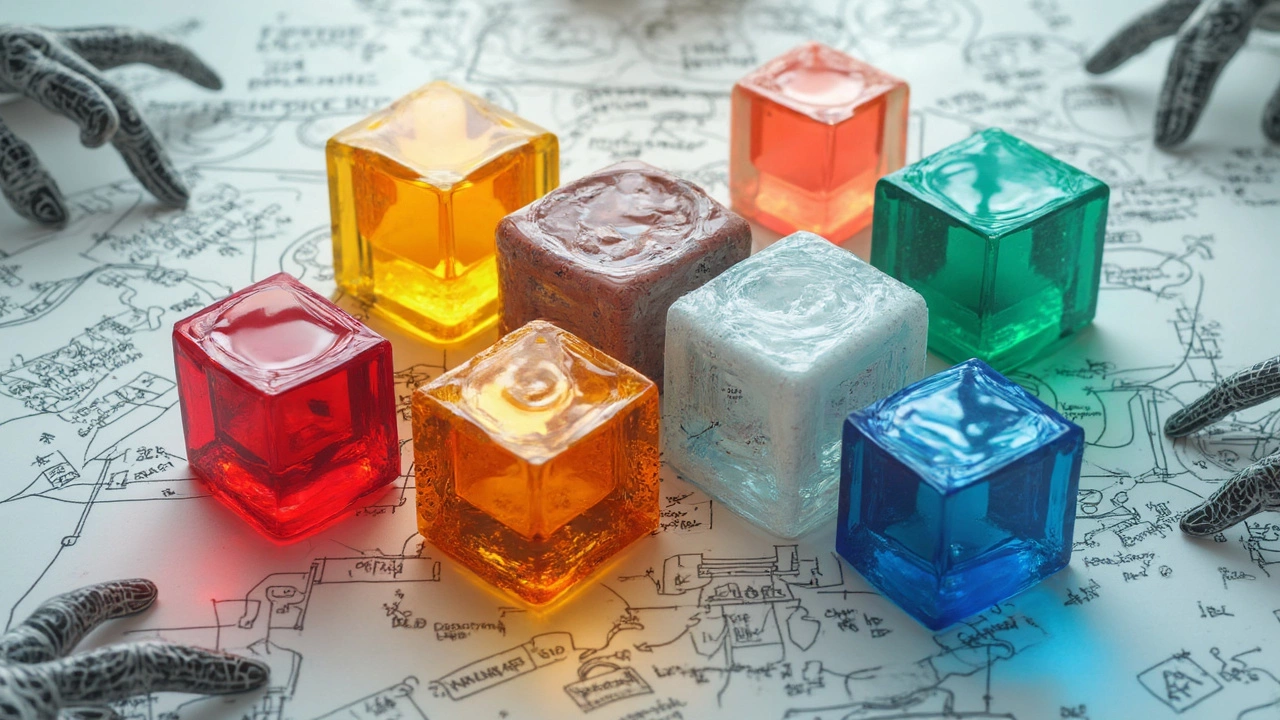
Real-World Examples: Where Premium Plastics Are Used
It's one thing to hear about tough, durable premium polymers—but where do they actually show up in day-to-day life or industrial work? The truth is, you’ve probably come across the highest quality plastic today without even realizing it.
In healthcare, medical devices absolutely have to be reliable. Polyether ether ketone (PEEK) and medical-grade polycarbonate are everywhere—from MRI-compatible surgical instruments to dental implants. These plastics keep their shape under crazy-high temperatures and don’t pick up germs like other materials might.
Look under the hood of any car built after 2000, and you’ll find ultra-high-molecular-weight polyethylene (UHMWPE) and tough nylon powering components like fuel lines and gears. They’re used because they cut down on weight—which means better gas mileage—and hold up against heat and grease without melting apart. One car manufacturer reported in 2023 that switching to high-quality nylon trims vehicle weight by up to 15 kilograms per car.
For electronics, ABS plastic is king when it comes to phone cases, laptop bodies, and even LEGO bricks. Those bricks you stepped on? That’s years of experimentation to get the mix exactly right—ABS from strong, consistent sources gives that perfect snap and last-for-decades toughness.
Even in the food industry, you’ll find food-grade polycarbonate and PET in reusable water bottles and baby bottles. These types need to be pure (no weird smells), super clear, and pass strict food safety rules. Fact: the global PET bottle market size crossed $30 billion in 2024, mostly thanks to stricter quality demands from big brands.
Industry | High-Quality Plastic Used | Main Benefit |
---|---|---|
Healthcare | PEEK, Polycarbonate | Heat resistance, hygiene |
Automotive | UHMWPE, Nylon | Lightweight, chemical resistant |
Consumer Electronics | ABS | Shock absorption, durability |
Food & Beverage | PET, Polycarbonate | Taste free, food safety |
If you’re thinking about sourcing for a business or your own project, always check where those top-performing plastics are already trusted. Industry use is the best stamp of approval.
Choosing the Right Plastic for Your Needs
It’s not about grabbing whatever’s cheapest or looks the toughest. To pick the highest quality plastic for your project, you need to get specific about what matters: where it’ll be used, what it’ll deal with, and what corners you just can’t cut.
Let’s start simple: If you’re making something that needs to survive the sun and nasty weather, like outdoor signage or playground equipment, you’ll want plastics like polycarbonate or UV-stabilized polyethylene. These won’t fall apart when summer hits. On the flip side, if you need materials for something medical—say, a piece that’ll go inside a hospital scanner—you’re looking for plastics like PEEK or medical-grade polypropylene, which are super pure and can take a beating from sterilization tools.
Here’s a no-nonsense checklist to help sort out your options:
- Strength & Flexibility: Going for impact resistance? Polycarbonate is a champ. Need flexibility but still want durability? Try polypropylene.
- Heat Resistance: ABS melts around 105°C, but things like PEEK can handle much hotter jobs (up to 250°C!) before getting wobbly.
- Chemical Resistance: Lots of cleaning or chemical exposure? PTFE (the stuff in non-stick pans) and PVDF don’t freak out when splashed with harsh stuff.
- Optical Clarity: For clear parts, acrylic and polycarbonate beat out most others, though polycarbonate is tougher if you need both strength and transparency.
- Certifications: If you’re in medical, food, or aerospace, double-check for certifications like FDA, NSF, or ISO ratings.
Here’s a quick comparison of some of the most common plastics for different needs:
Plastic | Best For | Notable Trait |
---|---|---|
Polycarbonate | Security windows, eyewear | Extreme impact resistance |
PEEK | Medical, aerospace | High heat & chemical resistance |
Polypropylene | Living hinges, food containers | Flexibility and fatigue resistance |
PTFE | Chem labs, cookware | Outstanding chemical resistance |
Acrylic | Display cases, lighting | Crystal-clear optics |
One more tip: Always talk to your materials supplier about your end use. They’ll often know about little tweaks (like blends or additives) that boost properties you care about. Remember, in plastic manufacturing, cutting corners on the material choice can backfire fast—so go for a plastic that fits your actual needs, not just what sounds cool or costs less upfront.
Expert Tips for Sourcing Reliable High-Quality Plastics
Getting your hands on highest quality plastic isn’t just about picking whatever’s labeled “premium.” The smartest manufacturing companies have a playbook for vetting suppliers and choosing the right polymers.
First, don’t just trust a supplier based on price or a flashy website. Real quality starts with certifications. If you're buying in bulk or need plastic for critical parts, always ask for ISO 9001 or IATF 16949 certifications. Those prove the manufacturer sticks to proven quality processes. For medical or food uses, look for FDA or USP Class VI compliance.
Test samples before locking in big orders. Ask the supplier for technical data sheets with numbers for tensile strength, heat tolerance, and impact resistance. Don’t just read the numbers—compare them to what your project actually needs. You’d be surprised how many times I’ve seen people order PLA for high-heat jobs just because it was cheap. The result? Warped or broken products after just a week of use.
- Check the plastic’s origin. Good suppliers are transparent about where the resin was made and if it’s virgin or recycled. Virgin resin usually means better consistency.
- Ask about batch traceability. If something goes wrong, you want to track down the issue fast and avoid repeating mistakes.
- Request documentation on additives and stabilizers. Sometimes extra ingredients boost performance, but other times—especially with knockoff suppliers—they’re used to hide flaws.
Sometimes it’s tempting to go with a less-known supplier just to save cash. If you do, run third-party tests. Plenty of labs will test melt flow rate, UV resistance, and even chemical make-up for a small fee.
Quality Checkpoint | Why It Matters |
---|---|
Certification (ISO, FDA, etc.) | Ensures global quality standards are met |
Technical Data Sheet | Shows material specs match your requirements |
Batch Traceability | Makes troubleshooting faster and easier |
Third-Party Testing | Verifies manufacturer claims are legit |
One last thing? Build relationships. When you find a supplier you can trust, stick with them. My wife, Priya, jokes I treat my resin rep’s number like a family heirloom. But seriously, long-term relationships get you better support, faster samples, and first dibs on new materials. That’s one edge every plastic manufacturing company wishes they’d claimed sooner.