6 Main Manufacturing Processes: Your Easy Guide
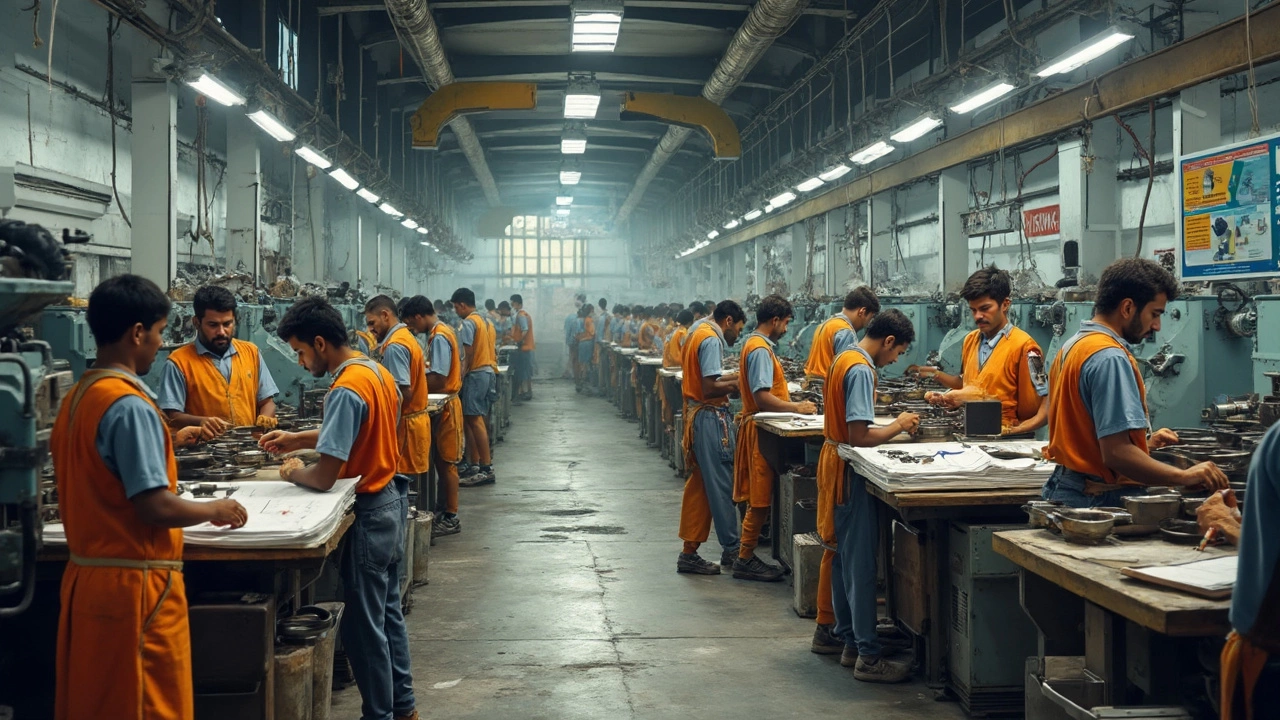
Imagine walking into a factory—you’ll probably see machines hammering, melting, cutting, or sticking things together. But did you know that almost everything is made using pretty much the same six basic processes? Understanding these isn’t just for engineers or factory owners. It actually helps if you’re thinking about starting a small business or even applying for a government scheme to boost your production.
Here’s the thing: every phone, car, kitchen pan, or even the screws in flat-pack furniture started with one of these core methods—casting, molding, machining, joining, forming, and additive manufacturing. Each offers a different way to get from raw material to finished product. Knowing which process fits best can save time, cash, and headaches down the line.
A surprising fact: India’s government has more than a dozen active schemes right now that support manufacturing, especially in small and medium businesses. Using the right manufacturing process could actually help you qualify for grants, training, or tax breaks. Think of it as choosing the best tool for the job—not just technically, but financially, too.
- What Are the Six Main Manufacturing Processes?
- A Closer Look: Real-Life Examples and Uses
- Government Schemes Powering Manufacturing
- Picking the Right Process: Tips and Mistakes to Avoid
What Are the Six Main Manufacturing Processes?
Every product you use—whether it’s your phone case or your kitchen chair—gets made using certain tried-and-true manufacturing processes. Out of all the ways to make stuff, six main types keep showing up everywhere.
- Casting: This one's about pouring liquid (usually metal or plastic) into a mold and letting it sit until it hardens. It’s how car engine parts and even toy figures are made. It’s a cheap way to make complex shapes quickly.
- Molding: Think plastic bottles and Lego bricks. Molding uses a similar idea to casting but mostly with plastics or soft materials—heated, squeezed into molds, and cooled. Injection molding is crazy popular in industries churning out lots of identical parts.
- Machining: Here, you start with a bigger chunk of material and chip away at it. Imagine carving out a statue—but with high-precision tools like lathes, drills, or CNC machines. It’s used to make parts that need tight tolerances, like metal gears for bikes or airplanes.
- Joining: Bringing things together—literally. Welding, soldering, glueing, or screwing parts together all count. Everything from your car frame to that flat-pack shelf you built last week uses joining.
- Forming: Here, you bend, stretch, or compress materials into shape. Rolling out dough is a home version of this, but factories are forming things like car doors (with stamping) and soda cans (with deep drawing).
- Additive Manufacturing: This is the fancy term for 3D printing. Instead of removing material, you add it layer by layer. It’s HUGE in prototyping and custom medical implants. This line of manufacturing processes is growing fast, especially since the cost of 3D printers has dropped like crazy in the last decade.
Process | Main Material | Main Example | Common Product |
---|---|---|---|
Casting | Metals, Plastics | Car engine block | Pots & pans |
Molding | Plastics | Injection-molded toys | Bottles |
Machining | Metals, Plastics | CNC-cut gears | Tool parts |
Joining | All | Welded frames | Furniture |
Forming | Metals | Stamped car panels | Cans |
Additive Manufacturing | Plastics, Metals | 3D-printed prototypes | Medical parts |
Picking the right type depends on what you want to make, how many you need, and the resources you’ve got. If you’re looking into government support for your manufacturing processes, certain schemes line up better with specific methods. For example, small-scale additive manufacturing outfits might tap into Make in India or MSME support schemes, which focus on new tech.
A Closer Look: Real-Life Examples and Uses
It can be hard to wrap your head around the main manufacturing processes without seeing them in action. So let’s break down what each one looks like in the real world, and where you’ve probably already bumped into their results.
- Casting: Think about engine blocks in cars or those heavy manhole covers on the street. Manufacturers pour liquid metal into a mold and let it cool. It’s one of the oldest tricks—factories in Gujarat, for example, churn out cast iron cookware using this classic method.
- Molding: Walk around your house and spot most plastic items. Water bottles, buckets, and even the cases for TVs are all made by injecting melted plastic into a mold. A company like Nilkamal does this at scale for plastic chairs that fill up every party hall you’ve ever visited.
- Machining: If you’ve got metal parts with exact shapes—like gears in a scooter or the lumps on your house keys—those started as solid metal and were cut and shaped by machines. Mysore is known for its machine-made tools that help make other things run smoothly.
- Joining: Look at any bicycle or ladder—that’s a bunch of metal tubes welded or bolted together. The massive steel bridges connecting Indian cities? Built from hundreds of parts joined together, often using welding as the main step.
- Forming: Ever watched someone shape rotis? Similar idea, but for metal—forming presses squish or bend materials. Car doors, soda cans, and metal pipes are all formed from flat pieces, especially with machines called “press brakes.”
- Additive Manufacturing: 3D printing is the face of this process. It’s a game-changer especially for making customized medical devices or those funky architectural models. Indian startups are printing spare parts on demand, reducing storage and waste.
Here’s a peek at how common these processes are in Indian factories based on government industry data:
Process | Main Example Product | Estimated Share of Factories (%) |
---|---|---|
Casting | Auto parts | 18% |
Molding | Plastic goods | 23% |
Machining | Machinery/tools | 21% |
Joining | Heavy structures | 14% |
Forming | Sheet metal items | 16% |
Additive Manufacturing | Prototypes | 8% |
Picking the right type of manufacturing isn’t just about what works. For small businesses trying to tap into government schemes, sticking to the proper way means fewer quality issues and sometimes even easier approval for funding. Always match the process with both the material and what you actually need from the product. Don’t guess, get advice from local manufacturing hubs or industry bodies—most are happy to share their insights.
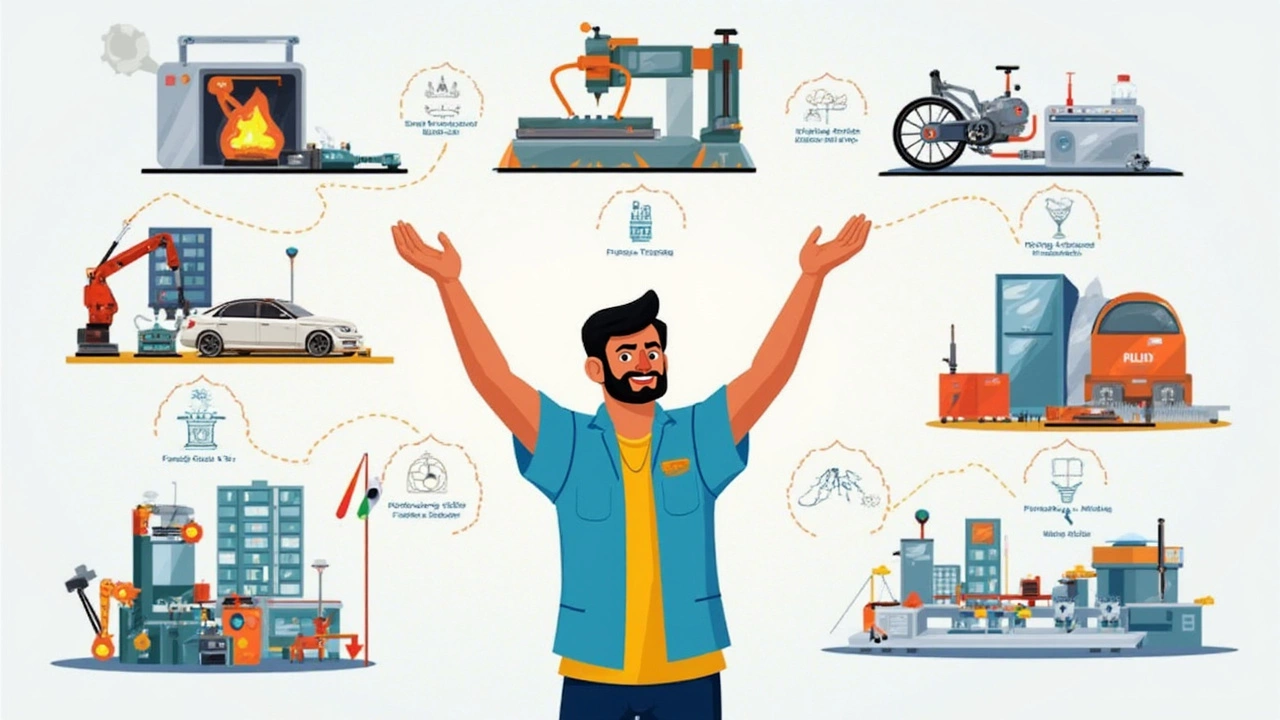
Government Schemes Powering Manufacturing
When it comes to manufacturing processes, getting financial help or benefits can make a world of difference for a business. That's where government schemes step in. Especially in countries like India and China, the government sees manufacturing as a backbone for jobs and exports. So, they roll out a buffet of schemes to bump up local manufacturing and make it easier for small and mid-size companies to modernize.
India, for example, has the Production Linked Incentive (PLI) scheme. This program offers direct incentives to companies for making goods locally. Covered sectors include electronics, auto, textiles, and even food processing. The idea is simple: the more you make, the bigger the government bonus.
The MSME scheme (Micro, Small and Medium Enterprises) is another biggie—if you’re producing parts using processes like casting or machining, you might qualify for cheap loans, free training, and even discounts on technology upgrades. They cut through a lot of the usual paperwork and legal hoops, so you can focus on actual production.
Here's some eye-opening data showing just how big an impact government support has had:
Scheme Name | Year Launched | Funds Allocated (INR crore) |
---|---|---|
PLI Scheme | 2020 | 1,97,291 |
MSME Support | 2006 (updated 2022) | 50,000+ |
If that sounds like a lot, that’s because it is. According to the Ministry of Commerce & Industry, "Schemes like PLI and Make in India are reshaping the country’s manufacturing landscape by encouraging industry leaders and new players alike."
"India’s production-linked incentive schemes could add $520 billion to manufacturing output over five years and create 6 million new jobs." — Economic Times, Dec 2023
But it's not just cash. These programs provide easier customs clearance, faster permissions, and even subsidies on power and water (which makes a real difference for any manufacturing process that eats up lots of energy, like forming or casting). There’s help for upskilling your team, too, so your people know how to use the latest machines and tech. If you’re aiming to tap into a government scheme, keep track of deadlines, required paperwork, and updates about new sector-specific incentives—the rules change fast and missing a date can mean losing out.
For anyone mapping out a new manufacturing business or looking to upgrade an old one, understanding these government schemes can be a game-changer. Don't ignore what's already out there—if you play your cards right, someone else might pay for your first big production run or that new 3D printer for your shop floor.
Picking the Right Process: Tips and Mistakes to Avoid
Choosing the right manufacturing process can make or break your project. It’s not just about what’s fastest or cheapest—it's about what delivers on quality, fits the job, and keeps headaches away down the road. Here’s what to watch for when making your pick.
- Match the process to the material: Not all processes work with all materials. For example, casting is great for metals and plastics, but you can’t cast wood. If you mess up here, you’ll waste time and money on repairs or rework.
- Consider the volume: Planning to make a one-off part or mass-produce a million units? Molding is awesome for high volume (think of all those toy cars), while machining is better for smaller runs or custom parts.
- Check complexity: Some designs are too complex for forming but perfect for additive manufacturing (like 3D printing). If you pick the wrong process, you might end up having to redesign your product—or worse, end up with lots of defective pieces.
- Plan for finishing: Think ahead about finishes—like painting, polishing, or coating. Some processes leave parts smooth and ready, others need extra steps. A shiny phone case is nice, but not if the process leaves it rough and needs heavy polishing.
And don’t forget the impact of government schemes. Some schemes will only support certain manufacturing processes. For example, schemes promoting “Make in India” often give perks for processes that use less energy or waste. Double-check the rules to get the most out of your application.
One common headache is jumping into a process because it’s popular, not because it fits. For instance, additive manufacturing sounds futuristic, but if you’re making thousands of simple metal bolts, it’s a slow (and expensive) choice. On the other hand, forging or machining would get those bolts ready faster and cheaper.
Here’s a quick look at which process often matches different needs. Notice how application shapes your choice:
Process | Best For | Common Products |
---|---|---|
Casting | Complex shapes, large volumes | Engine blocks, pipes |
Molding | High-volume plastics | Toy parts, bottle caps |
Machining | Small-volume, super precise | Prototypes, custom screws |
Joining | Assembly work | Car frames, furniture |
Forming | Simple shapes, metals | Cans, beams |
Additive Manufacturing | Complex, low-volume | Prototypes, custom tools |
Tip: Talk directly with suppliers or visit a local factory before deciding. Max, my dog, once chewed up a sample part made in the wrong material—lesson learned the hard way! Don’t let your project go to the dogs. Do your homework up front, and you’ll save way more pain later.