Biggest Manufacturing Waste Reduction Tips for Startups

In the bustling world of manufacturing, waste remains one of the most significant hurdles, especially for startups navigating the tightrope of costs and efficiency. Waste is the silent drain on the resources that could otherwise fuel innovation and growth. But fear not; understanding and tackling this issue can greatly enhance the prospects of any budding manufacturing business.
Embarking on this journey begins with identifying the various types of waste prevalent in manufacturing setups. These include overruns in material use, inefficient processes, unnecessary motion, and more—inefficiencies that stealthily gnaw at the bottom line. It’s crucial for startups to have a keen eye and an agile mindset towards optimizing each stage of production.
- Identifying Types of Waste
- Waste in Resource Consumption
- Production Process Inefficiencies
- Avoiding Overproduction
- Supply Chain and Logistics Management
- Strategies for Waste Minimization
Identifying Types of Waste
When it comes to minimizing waste in the realm of manufacturing waste, the first step lies in recognizing the myriad forms it takes. Within any production system, there are at least seven types of waste typically identified. These consist of transport, inventory, motion, waiting, overproduction, overprocessing, and defects. Each type can stealthily undermine the efficiency of an operation and inflate costs without providing any value to the customer.
Transportation waste occurs whenever goods or materials are moved unnecessarily, from one location to another, without adding any benefit. This could involve excess handling during various stages of production or ineffective facility layouts. Similarly, holding too much inventory is like pouring money into a black hole; it ties up valuable capital and can even lead to obsolescence of parts if not managed carefully.
Motion waste is often overlooked but is a critical aspect; it involves unnecessary movements by people or machines that do not contribute to product value. This could be due to improper workstation design or inefficient processes. Waiting, on the other hand, is that idle time when products are not moving or being processed, often resulting from synchronized workflow operations or reliance on external suppliers.
Overproduction stands as another significant issue; producing more than the actual demand can shield various other inefficiencies, resulting in higher storage costs or disposal problems. Overprocessing involves adding more features or activities than needed to meet customer demands, which can be avoided by focusing on simplicity and customer needs instead. Lastly, defects are perhaps the most obvious form of waste, as they call for rework, scrap, and ultimately lead to customer dissatisfaction.
Analyzing Common Waste Contributors
Digging deeper into these forms of waste unveils specific contributors that manufacturers can target for improvements. For example, some reasons that lead to transportation waste might include incorrect factory layouts or improper supply chain management strategies. Inventory issues may stem from inaccurate forecasting or lack of communication across departments.
The interesting thing is, corrections in one area often create opportunities elsewhere. Perhaps rectifying motion waste by installing equipment closer to workstations not only reduces unnecessary movements but also helps alleviate waiting times. As Lean Manufacturing concepts advocate, identifying and removing inefficiencies requires continuous assessment and a mindset open to constant improvements.
"Waste is anything other than the minimum amount of equipment, materials, parts, space, and workers’ time which are absolutely essential to add value to the product." - Taiichi Ohno, father of the Toyota Production System
Utilizing frameworks like Value Stream Mapping can expose these waste sources effectively by providing a visual guide to identify different steps in the process, offering a chance to trim the fat, so to speak, and achieve more streamlined operations.
The Road to Lean Transformation
In efforts to boost manufacturing efficiency, it’s essential to incorporate lean methodologies that emphasize eliminating waste at every turn. This journey often begins with creating a culture that prioritizes efficiency and advocates for autonomy among employees to identify and rectify wasteful practices continuously. Systematic training programs and communication channels can also ensure that all team members understand concepts surrounding waste reduction.
By embracing a proactive stance, manufacturers can not only minimize waste but also find avenues to enhance product quality, reduce lead times, boost customer satisfaction, and increase profitability. Within the competitive landscape of manufacturing startups, identifying and tackling these pervasive waste issues can lead to sustainable growth and a brighter future.
Waste in Resource Consumption
When we talk about waste in resource consumption, the spotlight gleams brightly on the unnecessary use of energy, water, and raw materials. In the manufacturing realm, mismanagement here often spells disaster. Every piece of material acquired has its cost, both monetary and environmental. If misused, it's like pouring precious assets away. Many firms find themselves embroiled in this silent crisis, unaware they are losing thousands, if not millions, on resources that don't end up contributing to their final product. By addressing this issue head-on, startups can significantly stretch their budgets and enhance operational efficiency.
Consider energy consumption, for instance. Manufacturing processes can guzzle vast amounts of electricity, steam, or natural gas. Several studies suggest that simply optimizing how machines run can slash this energy consumption dramatically. Sensors and automation, when applied smartly, can identify when equipment is idling and power it down. This not only saves energy but extends equipment lifespan and reduces maintenance costs. As business author Peter Drucker famously said,
“What gets measured gets managed.”By thoroughly analyzing where energy is spent, startups can craft intelligent strategies to conserve energy and cut costs.
Water, another precious commodity, often faces a similar fate. Many manufacturers use it in their processes without considering reuse or recycling possibilities. Implementing closed-loop water systems or investing in water treatment technologies, however, can save money and, crucially, align the business with sustainable practices. Far-reaching impacts, particularly concerning community good will and compliance with increasing environmental regulations, accompany this financial boon. A report by the World Bank estimated that efficient water use could reduce global demand in industrial sectors by around 20% by 2030.
Lastly, consider raw materials—an extensive area ripe for efficiency gains. Companies often overpurchase materials to avoid production hiccups, but this over-stocking results in excess inventory costs. Smart inventory management systems, which track usage and predict needs, can help maintain the delicate balance between excess and shortage. Plus, encouraging a culture of innovation within the team—where workers are constantly brainstorming ways to reduce material waste—can unveil groundbreaking processes and products. In structured brainstorming sessions, teams often find solutions that revolutionize their processes, moving them closer to zero waste goals. This culture not only conserves resources but can foster an environment where creative solutions thrive.
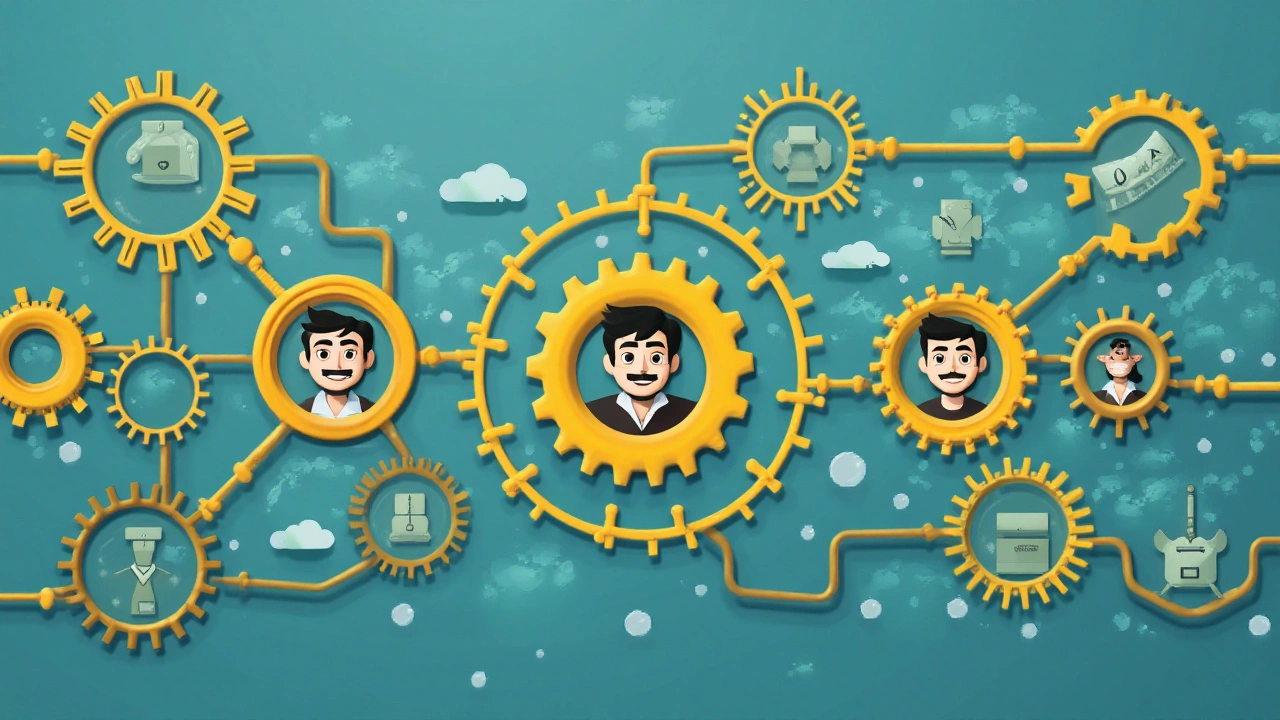
Production Process Inefficiencies
In the complex arena of manufacturing, inefficiencies in the production process often emerge as formidable barriers against achieving optimal efficiency. For startups, addressing these inefficiencies isn't merely beneficial; it's essential for survival and growth. But what are these inefficiencies, and how can they be mitigated or entirely eradicated?
Firstly, one of the most common sources of inefficiency in the production line is unplanned downtime. Machines breaking down or undergoing maintenance more frequently than anticipated can cause significant delays. A comprehensive preventative maintenance schedule is critical to avoid these pitfalls. By regularly inspecting and servicing machinery, you can prevent unscheduled stops that disrupt the flow of production. Implementing an IoT-based system for predictive maintenance can serve as a modern solution, offering real-time data on machine health and providing alerts before issues can spiral into full-scale malfunctions.
Another notable inefficiency comes from poor workflow design. When processes are not adequately streamlined, time is wasted in unnecessary movements within the production environment. To combat this, the principles of lean manufacturing can be applied. Techniques such as value stream mapping help companies visualize their production flow and identify bottlenecks or redundant steps that should be eliminated or optimized. By scrutinizing every step with an eye towards reducing waste, startups can significantly improve their production efficiency.
Human factors also contribute to production inefficiencies. Inadequate training or lack of motivation among employees can lead to errors, rework, and time loss. Investing in regular training programs ensures that workers are proficient with the machinery and procedures they must operate and helps cultivate a culture of continual improvement. Manufacturing waste is a concern any successful business must manage, and engaging your workforce in this mission can yield great returns.
Moreover, a lack of integration in the supply chain can lead to a mismatch between production and demand. This often results in either excess inventory or scarcity of necessary parts, both of which can throttle efficiency. Embracing an integrated supply chain management approach is a way to align production closely with demand. Digital tools that enable real-time tracking and dynamic adjustments can prove invaluable here.
"The journey to continuous improvement is ongoing. Each planned improvement cycle is a step toward increased efficiency." — Jeffrey Liker, author of 'The Toyota Way'
Implementing automation and robotics in the production line is yet another avenue to explore. Automation can take on repetitive and simple tasks with precision, freeing up human resources for more complex operations that require creativity and problem-solving skills. This shift not only accelerates the production rate but also minimizes human errors, an inherent form of waste.
Finally, measuring and analyzing performance metrics is vital. By establishing key performance indicators (KPIs) relevant to production, startups can continuously monitor and evaluate their operations' efficiency. It is through this constant scrutiny and adaptability that inefficiencies can be effectively reduced. Remember, the quest for manufacturing excellence in startups is not about a one-time effort but a relentless pursuit of perfection.
Avoiding Overproduction
Overproduction is one of the seven wastes identified by Taiichi Ohno within the Toyota Production System. It's not just about producing more than what is necessary; it’s a systemic issue that ripples across every corner of production and management. Avoiding overproduction requires a delicate balance between fulfilling market demands and maintaining operational efficiency. Startups, often constrained by limited capital and resources, need to pay special attention to the dynamics of overproduction as it impacts not only storage and inventory costs but also resource allocation and ultimately profitability.
A key strategy for combating overproduction is adopting a just-in-time (JIT) inventory system. By focusing on meeting immediate demands rather than predicting future ones, businesses can save significantly on storage costs and reduce waste. A JIT approach encourages producing only what is needed when it is needed, thus letting startups align production closely with demand patterns. Yet implementing JIT isn't without its challenges. A reliable forecasting method and resilient supply chains are crucial for ensuring that inputs required for production are timely and sufficient.
"The simplest way to eliminate waste is to allow the system to reveal it and then force it to be removed," said Taiichi Ohno, the father of Toyota’s Production System, emphasizing the importance of real-time insights in waste management.
To avoid overproduction, startups should also consider deploying demand-driven production methods, where incentives are tied directly to current demand, not just projections. For instance, employing tools like Kanban can help monitor production progress and manage workflow efficiently. Kanban systems can visually signal when inventory is running low, prompting action to refill only what’s needed—preventing excess and facilitating smooth production flows. Additionally, startups should cultivate agile production environments, enabling adaptability in cases of sudden demand spikes or drop-offs. A flexible floor plan and multifunctional teams can quickly ramp up or down production levels without creating bottlenecks or waste.
Leveraging Technology
Today’s tech-driven world offers a wealth of tools that can precisely monitor and analyze production metrics. With the advent of AI and machine learning, startups can now predict demand with greater accuracy. This technological edge helps in curbing overproduction by fine-tuning manufacturing schedules in real-time. Predictive analytics, paired with a robust manufacturing execution system (MES), can act as the backbone of a proactive strategy against overproduction. Such systems integrate data points from across the supply chain, delivering actionable insights to decision-makers.
Moreover, integrating Internet of Things (IoT) devices into manufacturing equipment presents another layer of real-time monitoring capabilities. These smart devices collect data from various production stages, feeding into analytics platforms to provide comprehensive production health insights. Implementing these systems may seem costly initially, but the long-term efficiencies gained often outweigh the initial investment, proving particularly beneficial for startups striving to maximize resource use and minimize waste. And for those looking at greener manufacturing, reducing overproduction is a direct pathway to sustainability, reinforcing brand reputation as environmentally conscious.
To encapsulate, avoiding overproduction relies heavily on a blend of strategic foresight, technological adaptation, and cultural integration within startups. By nurturing a close-knit alignment between marketing, sales, and manufacturing departments, businesses can ensure everyone is on the same page concerning customer demands and market trends. This collaborative mindset, combined with astute use of technology, paves the way for not just averting overproduction but also fostering an efficient and responsive manufacturing culture.
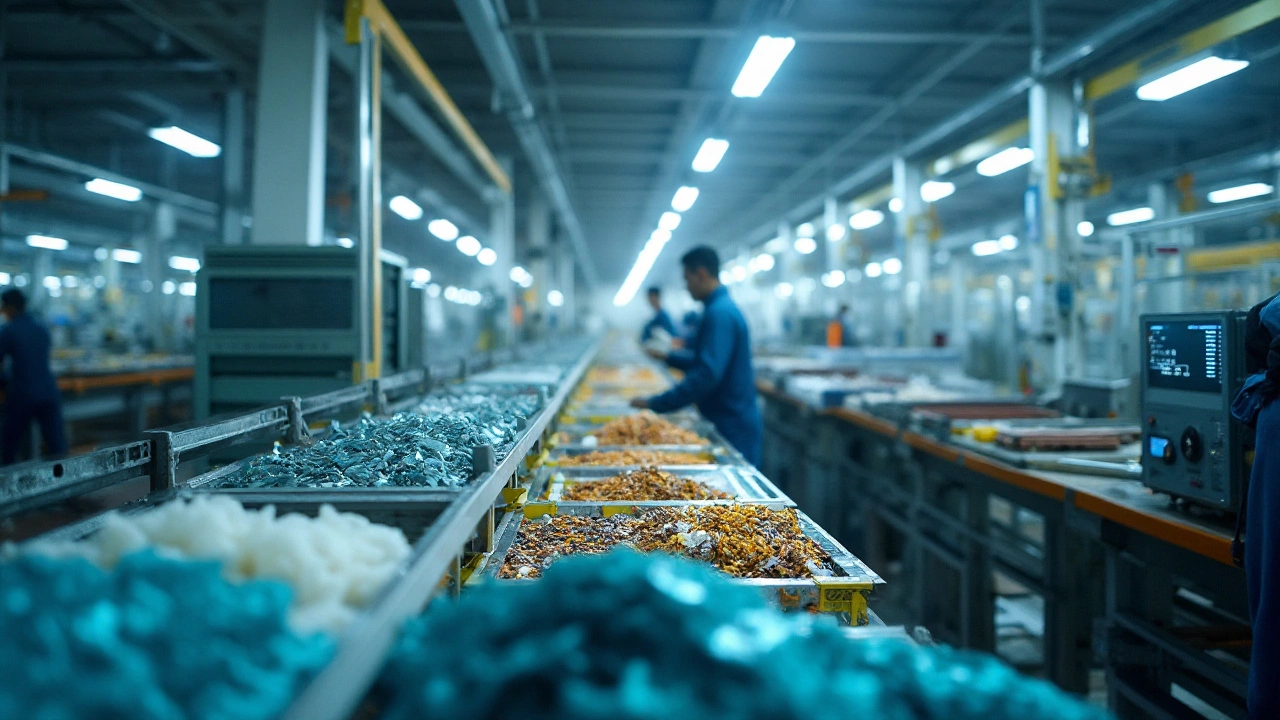
Supply Chain and Logistics Management
In the intricate dance of modern manufacturing, manufacturing waste often starts or ends in the realm of supply chain and logistics. A well-managed supply chain acts as the backbone of efficiency, streamlining operations from raw material acquisition to final product delivery. For startups, aligning supply chain strategies with production needs is not merely beneficial but essential. Ensuring that materials arrive just in time for production minimizes storage costs and reduces excess inventory, a common source of waste. Effective logistics management plays a vital role in optimizing these processes by decreasing transportation costs and times, which directly impacts the bottom line. The ability to predict demand accurately and communicate seamlessly with suppliers can spell the difference between profit and loss, especially in the competitive, fast-paced manufacturing sector.
Effective supply chain management involves consistently reassessing supplier relationships and leveraging technology to optimize each link. Utilizing digital platforms for real-time inventory tracking can offer startups a significant edge, significantly reducing manufacturing waste. Developing resilient supply chains that can quickly adapt to unforeseen disruptions ensures less raw material goes unused and prevents delays that can pile on costs. A notable point of reference is the agility seen in some automotive sectors, where just-in-time production models have been employed to significant effect, lowering costs and improving resource utilization.
"A strong supply chain begins with strong relationships," said Joe Smith, a logistics expert quoted in Manufacturing Today. "It’s about collaboration and transparency that drives innovation and efficiency across industries."
Furthermore, sustainable practices within supply chains are becoming increasingly crucial as environmental concerns mount. Startups that integrate eco-friendly transportation options, such as selecting greener vehicles or optimizing delivery routes, position themselves for favorable views from environmentally-conscious consumers and partners. These efforts not only reduce carbon footprints but also reflect positively in operational costs over time as energy prices rise. Firms must intentionally structure their logistics to adapt swiftly to market changes, which tends to eradicate wastage of time and resources. The strategic use of technology, from IoT sensors for monitoring shipments to blockchain for securing and streamlining transactions, is crafting the future landscape of supply chain management.
To distill logistics and supply chain management strategies that cut waste, startups might consider adopting the following practical steps:
- Regularly audit supply chain performance for inefficiencies and areas of improvement.
- Implement advanced inventory management systems to precisely align stock levels and prevent overproduction.
- Cultivate close partnerships with suppliers to ensure reliability and quality, aiming for long-term contracts that offer price stability.
- Invest in training for logistics personnel to keep abreast of best practices in reducing transportation waste.
- Explore and integrate renewable energy sources into logistic operations to cut down on emissions and operating costs.
Adopting these strategies not only minimizes waste but also sets the stage for scalability and adaptability as startups grow. As the manufacturing landscape evolves, those prepared with robust supply chains and well-managed logistics will undoubtedly lead in efficiency and sustainability.
Strategies for Waste Minimization
In the pursuit of sustainable operations, startups in the manufacturing sector can adopt several effective strategies for waste minimization. One prominent method is the integration of lean manufacturing principles, which focuses on creating more value with less work by eliminating redundant processes and optimizing the use of resources. Lean strategies not only streamline operations but also significantly reduce waste by precisely identifying areas where inefficiencies lurk. Implementing lean involves a thorough analysis of each production phase, ensuring every step adds value and contributes to the end product without unnecessary excess.
Technology plays a pivotal role in waste reduction strategies. Advanced data analytics and IoT solutions enable manufacturers to monitor production processes in real time, adjusting operations on the fly to prevent waste before it occurs. These technologies allow insights into where resources are being utilized ineffectively, empowering businesses to make informed decisions. The adoption of automation, for instance, reduces human error and increases precision, which directly impacts the reduction of waste materials. According to a report from McKinsey, manufacturers that invest in digital technology innovations can see waste reductions by up to 20%.
"Waste is a product of inefficiency, and on the path to minimizing waste, technology is an essential tool that assists firms in achieving lean goals with minimal effort," says James Womack, co-founder of the Lean Enterprise Institute.
Another avenue for minimizing waste is enhancing supply chain efficiency. By fostering close relationships with suppliers and working collaboratively, startups can synchronize supply chain operations to better match production needs. Strategies such as just-in-time inventory management, which ensures materials and products are only ordered as needed, can prevent accumulation of surplus stock that eventually leads to waste. It's a proactive approach that requires good forecasting and communication but reaps significant benefits in reducing excess. In this context, supply chains should also aim at being more sustainable through the integration of eco-friendly practices and materials.
Engaging employees in waste reduction initiatives also stands as an essential strategy. Training workers to understand and recognize waste, along with empowering them to propose improvements, fosters a culture of constant optimization. This employee-driven approach not only improves morale but also embodies the agile nature of a startup, where every member’s contribution is vital. Regular workshops and interactive sessions focused on waste identification and reduction can help sustain long-term minimization goals.
Finally, cross-industry collaborations can introduce innovative ideas and strategies for waste minimization in manufacturing. By connecting with partners from different sectors, startups can explore novel ways to repurpose waste or leverage best practices that might not have been considered. Such partnerships can lead to shared knowledge, pooled resources, and even expanded market opportunities.
Companies can also investigate ways to recycle waste within the production cycle itself, reusing offcuts and by-products in other parts of the manufacturing process. Not only does this approach decrease waste disposal costs, but it also creates new input material, cutting down on the need for fresh resources. Keeping an eye on holistic resource management, informed by detailed data patterns and employee insights, spurs efficient and sustainable manufacturing operations capable of competing in today's eco-conscious market.